Plant Engineering :
We leverages the expertise for the economical use of land, building, space, with arrangement of physical facilities such as machinery, equipment, furniture, & utilities etc. to facilitate minimal material movement & handling. In turn, getting the flexibility of operations, employee convenience, & promoting safety. Plant engineering is the designing of the entire facility and not only the process. It deals with the design, realisation, and maintenance of technical plants. We assure our clients with the application of the best in class engineering principles, techniques, & technologies, helping them to optimise the performance, efficiency, & safety of industrial processes.
Sidebar Menu
🔹Domain
- 📌 RFQ Management
- 📌 Industrial Engineering
- 📌 Plant Engineering
1. Design & Construction
As an integrated system, a process of creating the description of a new facility, usually represented by detailed plans and specifications.
Scope of Work –
- Identification of activities and resources
- Involvement of the architects and engineers for the making of the detailed design and drawing
- Mapping of the conditions peculiar to a specific site ( weather, labour supply, local building codes etc.)
- Formal approval process for the final plans and designs, with the client
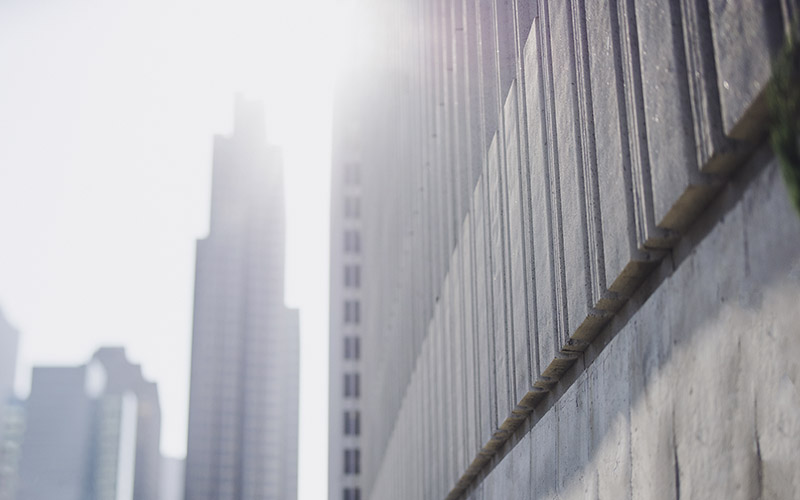
6. Initiation & implementation of the civil and said activities
7. Dynamic changes during implementation as per situational demand
2. Maintenance & Reliability
We can be a source for supporting in all of the maintenance engineering related solutions comprising management, planning, and budgeting.
Reliability with the application of technical skills and ingenuity to the correction of equipment problems, causing excessive production downtime and maintenance work, focussing on the elimination of repetitive failure.
“Effective maintenance contributes to improved reliability”
Scope of Services
- Preventive Maintenance – Defining regular and periodic tasks according to predefined schedules. Aiming prevention of equipment failures and improving the life span of the asset by addressing the potential issues.
- Corrective Maintenance – Restoration of the equipment to its normal operating conditions from an identified issue or failure. Aiming to minimise the downtime and restoring the planned availability by quick restoration of the functionality.
- Pre determined Maintenance – Analysis of the historical data of the equipment and industrial standards to pre defined the activities. It involves routine servicing, & part replacement, defining the consistency with pro active approach.
- Condition Based Maintenance – Real time assessment of the asset with diagnostic tools to monitor the specific or threshold condition, thereby planning the maintenance activities.
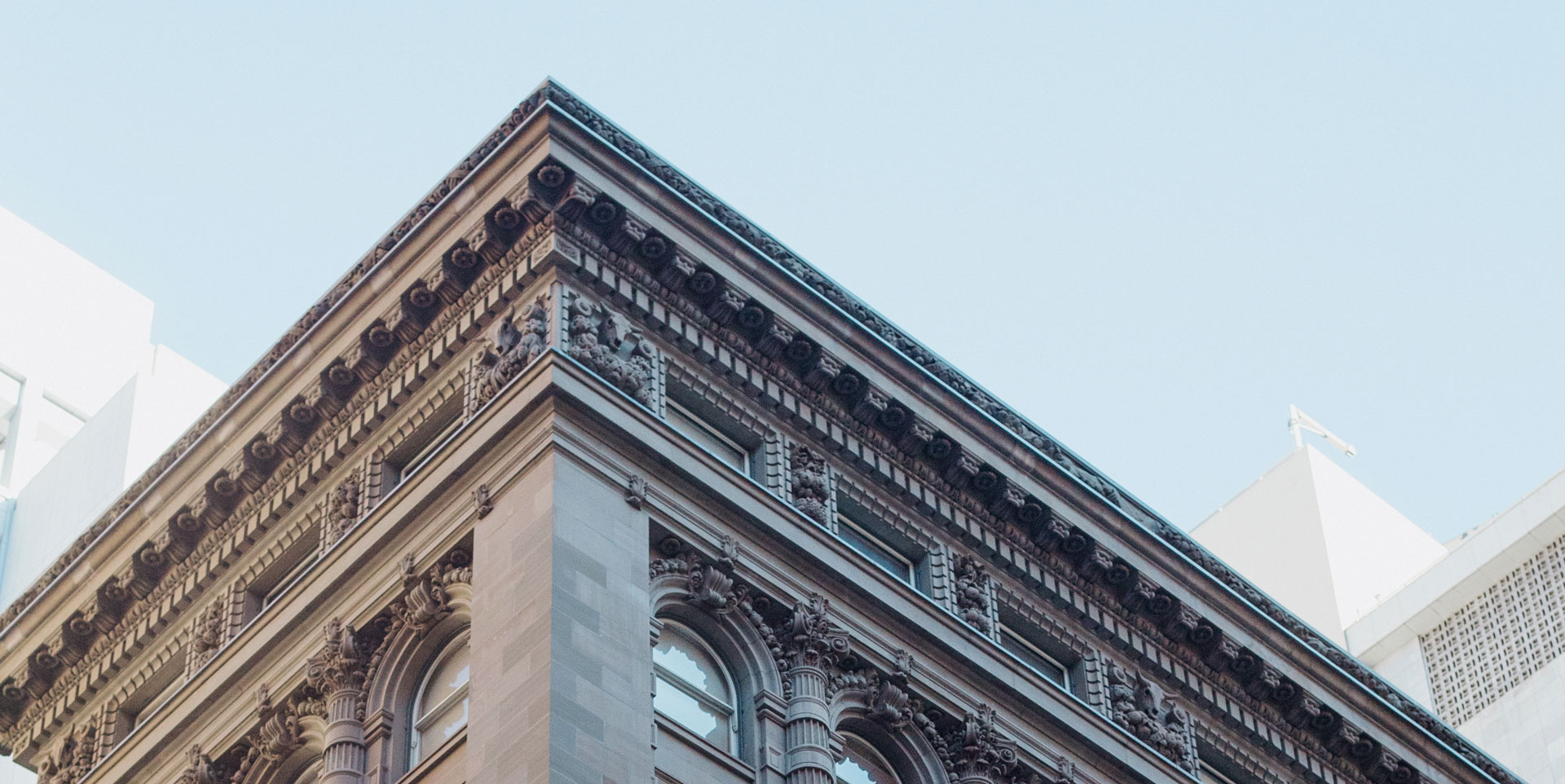
- Predictive Maintenance – With assessment of condition based maintenance and further analysis of the historical data, trends, & patterns, predictive maintenance algorithms identify potential issues and recommend the planning of maintenance activities. This helps in minimising the unplanned downtime, in optimising the maintenance resources and in improving the asset availability and reliability.
- Reactive Maintenance – In the emergency and critical situations, on-time support, for the unexpected failure of the equipment, for which immediate action is required to restore the functionality. It depends on the situational demands under crisis management.
- Reliability Metrics – Evaluation of the failure likelihood and functional consistency of the asset with standard metrics – Failure Rate, Mean time between failures, Mean time to failures, & Mean time to repair.
- Maintenance Budgeting – We support in the making of the maintenance budget, based on the business objectives, effective resource allocation, continuous improvement, workforce requirements, skill development, spare parts inventory, consumable inventory, tools’ inventory. It helps in deciding the key performance indicators and improving the maintenance effectiveness in line with organisational goals.
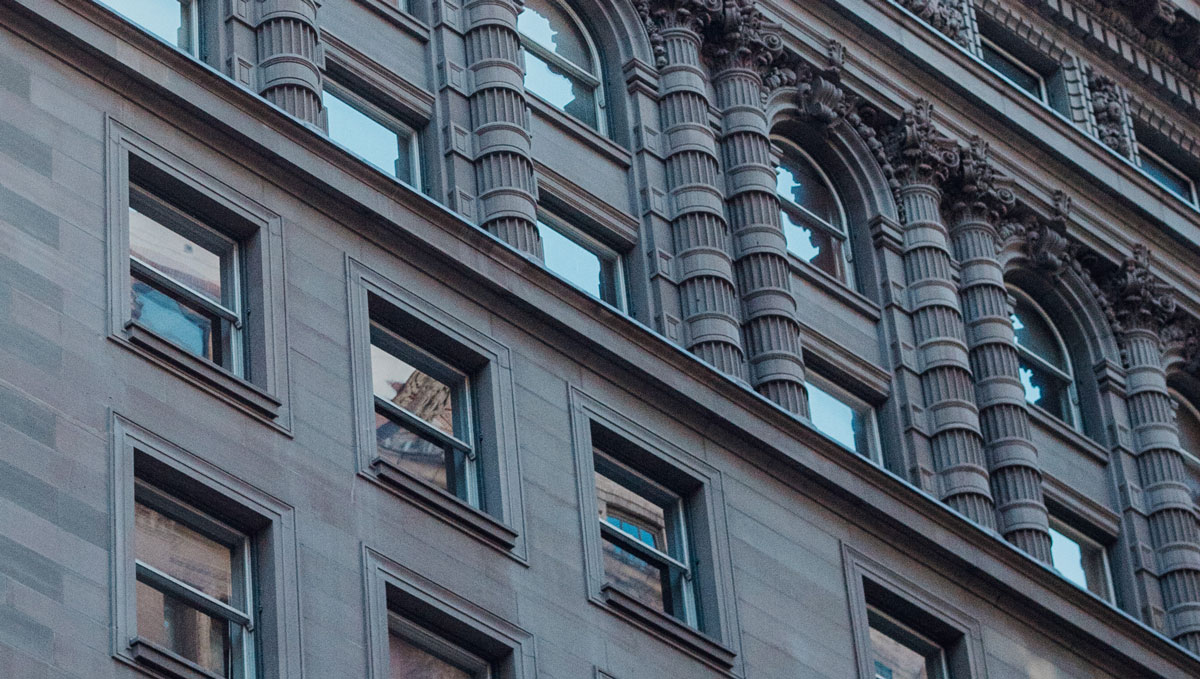